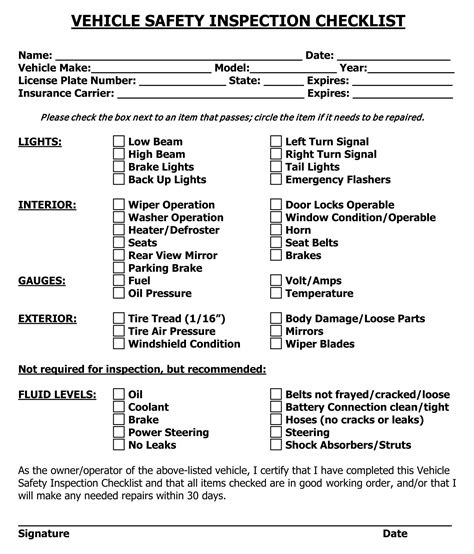
Welcome to today’s blog post where we will be discussing the importance of regular air suspension maintenance. If you own a vehicle equipped with an air suspension system, it is crucial to properly maintain it to ensure optimal performance and safety. In this article, we will guide you through the step-by-step process of checking air pressure, inspecting and replacing air springs, examining and cleaning air lines and fittings, as well as inspecting and lubricating suspension components. We will also cover checking for leaks, inspecting and tensioning suspension bolts, checking and adjusting ride height, and regularly inspecting and replacing shock absorbers. Stay tuned for valuable tips and insights on keeping your air suspension system in top condition.
Importance of Regular Air Suspension Maintenance
Regular air suspension maintenance is crucial for ensuring the proper functioning and longevity of the suspension system in your vehicle. Neglecting this important aspect of vehicle maintenance can lead to various issues, including poor ride quality, reduced handling performance, and even safety hazards. By taking the time to regularly inspect and maintain your air suspension components, you can avoid such problems and enjoy a smoother and safer driving experience.
One of the key aspects of air suspension maintenance is checking the air pressure in the system. Adequate air pressure is essential for optimal suspension performance. By using a pressure gauge, you can easily measure the air pressure in each air spring. If the pressure is too low, you can use an air compressor to add air. On the other hand, if the pressure is too high, you can release some air to achieve the desired levels. Keeping the air pressure within the recommended range is vital for ensuring a comfortable and controlled ride.
Inspecting and replacing air springs is another important part of regular air suspension maintenance. Air springs, also known as air bags or air bellows, are responsible for supporting the weight of the vehicle and providing a smooth and cushioned ride. Over time, these springs can wear out or develop leaks, leading to a compromised suspension system. By closely examining the air springs for any signs of damage or wear, you can identify and replace them as needed to maintain the proper functioning of your air suspension system.
Examining and cleaning air lines and fittings is yet another crucial aspect of air suspension maintenance. Air lines and fittings connect various components of the air suspension system and are prone to debris and dirt buildup. Regularly inspecting these lines and fittings can help identify any clogs, leaks, or loose connections that may affect the overall performance of the system. By cleaning or replacing any faulty air lines or fittings, you can ensure that the suspension system operates smoothly and without any issues.
Checking Air Pressure in the Suspension System
Checking air pressure in the suspension system is an essential part of regular air suspension maintenance. Proper air pressure is crucial for ensuring optimal performance and safety of the suspension system. By maintaining the correct air pressure, you can prevent unnecessary wear and tear on the components and enhance the overall longevity of the system.
One of the easiest ways to check the air pressure in the suspension system is by using a tire pressure gauge specifically designed for air suspension. These gauges are equipped with the necessary fittings to measure the pressure accurately. Begin by locating the air valve on each air spring of the suspension system. Insert the gauge’s nozzle firmly onto the air valve and press down to ensure a proper seal.
Once the gauge is connected, read the pressure measurement on the gauge’s display. Compare the reading with the manufacturer’s recommended air pressure for your particular vehicle and suspension system. It’s important to note that different vehicles may have different pressure requirements, so always refer to the manufacturer’s guidelines.
After checking the pressure, adjust the air pressure if necessary. If the reading is below the recommended pressure, you will need to add air to the suspension system. Conversely, if the reading is above the recommended pressure, you will need to release some air until it reaches the correct level. This can be done using a small air compressor or by using the release valve on the air spring.
Advantages of Checking Air Pressure in the Suspension System | Disadvantages of Neglecting Air Pressure Checks |
---|---|
|
|
By regularly checking the air pressure in the suspension system, you can enjoy various advantages. Maintaining optimal suspension performance ensures a smooth and comfortable ride. With the correct air pressure, you can enhance the handling and stability of your vehicle, especially during cornering and braking. Additionally, maintaining the recommended air pressure helps improve fuel efficiency, reducing your overall fuel consumption.
On the other hand, neglecting air pressure checks can result in several disadvantages. Insufficient air pressure can lead to uneven tire wear and compromised handling, making your journey less safe. Incorrect air pressure can also impact fuel efficiency, causing unnecessary expenditure. Moreover, neglecting these checks can lead to potential damage to the suspension system, resulting in costly repairs and replacements.
Regularly checking the air pressure in the suspension system is a simple yet important aspect of maintenance. By investing a few minutes to ensure the correct pressure, you can enjoy improved performance, safety, and longevity of your air suspension system.
Inspecting and Replacing Air Springs
When it comes to maintaining your air suspension system, one important task is inspecting and replacing air springs. Air springs, also known as airbags or air bellows, play a critical role in supporting the weight of your vehicle and providing a smooth and comfortable ride. These springs are typically made of durable rubber and are designed to withstand the constant pressure and flexing that occurs during suspension movement.
Inspecting your air springs regularly is essential to ensure they are in good working condition. Start by visually inspecting them for any signs of damage, such as cracks, tears, or leaks. Pay attention to the mounting brackets as well, as they should be securely attached. If you notice any issues, it is crucial to replace the air springs immediately to prevent further damage to your suspension system.
When it comes to replacing air springs, it is recommended to refer to your vehicle’s manufacturer guidelines or consult a professional mechanic. The process may vary depending on the make and model of your vehicle. However, some general steps can be followed. Begin by safely raising and supporting your vehicle. Release the air pressure from the suspension system using the appropriate method, such as disconnecting the air line or removing the airbag valve. Then, remove the old air spring by detaching any retaining bolts or clamps. Finally, install the new air spring and secure it properly, ensuring all connections are tight and secure.
Inspecting and replacing air springs should be part of your routine maintenance to prolong the life of your air suspension system and ensure optimal performance. By addressing any issues promptly and replacing worn-out or damaged air springs, you can prevent costly repairs and avoid compromising your vehicle’s ride comfort and stability.
Air suspension systems are complex and require regular maintenance to remain in top condition. Inspecting and replacing air springs is just one of the many tasks you need to consider. Remember to consult your vehicle’s owner manual or seek professional guidance to ensure you are performing the proper maintenance procedures.
Examining and Cleaning Air Lines and Fittings
Regular maintenance of air suspension systems is crucial to ensure optimal performance and longevity. One essential aspect of this maintenance is examining and cleaning the air lines and fittings. The air lines are responsible for carrying the pressurized air between various suspension components, while the fittings connect these lines to the relevant parts. Over time, these lines and fittings can accumulate debris, dirt, and moisture, compromising their functionality. It is imperative to regularly inspect and clean them to avoid potential issues.
In order to examine the air lines and fittings, start by visually inspecting them for any signs of damage or wear. Look for cracks, leaks, corrosion, or loose connections. Any abnormalities should be addressed promptly to prevent further damage. Additionally, make sure to check the rubber seals and gaskets for signs of deterioration or leaks. If you come across any damaged parts, they should be replaced with high-quality replacements.
After inspecting the air lines and fittings, the next step involves cleaning them. Begin by disconnecting the air lines from the fittings using the appropriate tools. Use compressed air to blow out any accumulated dirt or debris from both the lines and the fittings. Be mindful not to use excessive pressure as it can damage the components. Next, use a mild detergent or solvent and a soft brush to clean the surfaces of the fittings and the ends of the air lines. Rinse them thoroughly with water and dry them completely before reassembling.
Ensuring the cleanliness of the air lines and fittings is essential for maintaining the overall performance and safety of the air suspension system. By regularly examining and cleaning these components, you can prevent potential issues such as leaks, obstructions, or faulty connections. Moreover, this practice helps to prolong the lifespan of the suspension system. Make sure to prioritize this aspect of maintenance along with other essential tasks to enjoy a smooth and reliable ride.
Inspecting and Lubricating Suspension Components
Regular inspection and lubrication of suspension components is a crucial maintenance task that helps ensure the longevity and optimal performance of your vehicle’s air suspension system. By inspecting and lubricating these components, you can proactively identify any potential issues and prevent costly repairs down the line.
Why is it important?
Inspecting and lubricating suspension components can help prevent premature wear and tear, reduce friction, and enhance the overall functionality of the system. Over time, the constant movement and pressure exerted on the suspension components can cause them to become dry, rusty, or corroded. This can lead to increased friction, noise, and even decreased ride comfort.
What components should you inspect and lubricate?
Component | Inspection | Lubrication |
---|---|---|
Control Arms | Check for cracks or damage. | Apply lubricating grease to the bushings. |
Ball Joints | Inspect for excessive play or wear. | Apply lubricating grease to the fittings. |
Sway Bar Links | Look for any signs of wear or looseness. | Apply lubricating grease to the joints. |
Control Arm Bushings | Check for cracks or deterioration. | Apply lubricating grease to the bushings. |
How often should you inspect and lubricate?
It is recommended to inspect and lubricate suspension components every 12,000 to 15,000 miles or at least once a year, depending on your driving conditions. However, if you frequently drive on rough roads or encounter extreme weather conditions, more frequent inspections may be necessary.
Tips for inspection and lubrication:
- Always refer to your vehicle’s owner’s manual for specific instructions and recommendations.
- Use high-quality lubricating grease that is recommended for automotive suspension systems.
- Clean the components before lubricating to remove any dirt or debris that may hinder proper lubrication.
- Inspect for any signs of leaks, damage, or excessive wear during the lubrication process.
- Consider seeking professional assistance if you are unsure about performing the inspection and lubrication yourself.
By regularly inspecting and lubricating suspension components, you can ensure the smooth operation and longevity of your vehicle’s air suspension system. This simple maintenance task can save you time and money in the long run, while also enhancing your driving experience and safety.
Checking for Leaks in the Air Suspension System
Regular maintenance is crucial to ensure the smooth functioning of your air suspension system. Among the various maintenance tasks, one important aspect is checking for leaks. Any leaks in the system can lead to a loss of air pressure, which in turn can result in a bumpy and uncomfortable ride. Moreover, if left unaddressed, leaks can cause detrimental damage to the suspension components. Therefore, regularly inspecting and resolving any leaks should be an integral part of your maintenance routine.
One effective way to check for leaks in the air suspension system is by performing a visual inspection. Start by examining all the air lines and fittings connected to the suspension system. Look for any visible signs of wear, corrosion, or damage. Cracked or deteriorated air lines are often indicative of a leak. Additionally, inspect the air springs for any signs of leakage or damage. If you notice any issues, it is essential to replace the faulty components promptly.
Aside from the visual inspection, it is also recommended to perform a leak test to ensure the integrity of the air suspension system. This can be done by pressurizing the system and monitoring the air pressure levels. Start by inflating the system to the manufacturer’s recommended pressure level and then turn off the engine. Monitor the pressure gauge for any significant drops in pressure. If the pressure decreases rapidly, it indicates a leak in the system.
- Regularly inspect and replace worn-out air lines and fittings.
- Examine air springs for signs of leakage or damage.
- Perform a leak test by monitoring air pressure levels.
Importance of Regular Air Suspension Maintenance | Checking Air Pressure in the Suspension System | Inspecting and Replacing Air Springs |
---|---|---|
Content on the importance of regular maintenance | Content on checking air pressure in the system | Content on inspecting and replacing air springs |
Inspecting and Tensioning Suspension Bolts
The suspension system of a vehicle plays a crucial role in providing a smooth and comfortable ride. Among the various components that make up this system, suspension bolts are often overlooked but are equally important for maintaining optimal performance and safety. In this blog post, we will explore the importance of inspecting and tensioning suspension bolts as part of regular maintenance.
One of the main reasons for inspecting suspension bolts is to ensure that they are properly tightened. Over time, the constant vibrations and movements experienced by the vehicle can cause the bolts to loosen. Loose bolts can lead to various issues, such as noise, vibrations, and even compromised handling. Therefore, it is essential to regularly tension these bolts to the manufacturer’s specified torque settings.
Inspecting suspension bolts should also involve checking for any signs of wear or damage. Excessive wear or corrosion can weaken the bolts, compromising their strength and ability to hold components securely in place. During the inspection, it is important to pay attention to any signs of rust, deformation, or missing hardware. Any bolts showing signs of deterioration should be replaced immediately to prevent potential failure.
A well-maintained suspension bolt not only ensures the proper functioning of the suspension system, but it also contributes to overall vehicle safety. Therefore, regular inspections and proper tensioning of these bolts are essential to prevent any potential hazards on the road. Inspecting and tensioning suspension bolts should be included as part of routine maintenance, especially if you frequently travel on rough terrains or encounter severe driving conditions.
In conclusion, the inspection and tensioning of suspension bolts should not be overlooked when maintaining a vehicle’s suspension system. Regularly checking for proper tightness and signs of wear or damage can prevent potential issues and ensure a safe and comfortable driving experience. Make sure to include this important task as part of your regular maintenance routine to keep your suspension system in optimal condition.
Checking and Adjusting Ride Height
One important aspect of maintaining a vehicle’s air suspension system is checking and adjusting ride height. Ride height refers to the distance between the vehicle’s chassis and the ground. It is crucial to ensure that the ride height is properly set as it not only affects the vehicle’s overall performance but also plays a significant role in passenger comfort and safety.
Regularly checking and adjusting the ride height is essential to prevent issues such as uneven tire wear, poor handling, and compromised stability. When the ride height is too low, the vehicle may experience bottoming out, leading to damage to the suspension components and a harsh ride. On the other hand, if the ride height is too high, it can cause excessive body roll, reduced steering response, and increased braking distance.
There are different methods for checking and adjusting ride height, depending on the type of air suspension system installed in the vehicle. One common approach is to measure the distance between specified points on the chassis and the ground using a tape measure or a ride height gauge. These specified points are usually marked on the vehicle’s body or outlined in the manufacturer’s manual. By comparing the measured distance with the recommended ride height range provided by the vehicle manufacturer, adjustments can be made to ensure proper ride height.
Benefits of Checking and Adjusting Ride Height
- Improved handling and stability
- Better road grip and traction
- Reduced tire wear
- Enhanced passenger comfort
Table: Recommended Ride Height Range
Vehicle Model | Front Ride Height (inches) | Rear Ride Height (inches) |
---|---|---|
Sedan A | 10.5 – 11.5 | 11.0 – 12.0 |
SUV B | 12.0 – 13.0 | 12.5 – 13.5 |
Truck C | 11.5 – 12.5 | 12.0 – 13.0 |
Regularly checking and adjusting ride height not only ensures optimal performance and safety but also helps prevent unnecessary wear and tear on various suspension components. It is recommended to consult the vehicle’s manual or seek professional assistance if any difficulties or uncertainties arise during the inspection and adjustment process. By maintaining the correct ride height, drivers can enjoy a smooth and comfortable ride while prolonging the lifespan of their vehicle’s air suspension system.
Regularly Inspecting and Replacing Shock Absorbers
Regularly inspecting and replacing shock absorbers is an essential part of maintaining a smooth and comfortable ride in your vehicle. Shock absorbers, also known as dampers, play a crucial role in controlling the movement of the suspension system and preventing excessive bouncing or vibration. Over time, these components may wear out or become damaged, leading to decreased performance and increased risk of accidents. By regularly inspecting and replacing shock absorbers, you can ensure optimal vehicle handling, improved braking, and enhanced overall safety.
Inspecting shock absorbers involves visually examining them for signs of damage or wear. Look for leaks, corrosion, or any signs of fluid leakage around the shock absorber body or mounting points. Inspect the rubber bushings and mounting bolts for any signs of deterioration or loosening. Additionally, pay attention to any unusual noises or excessive bouncing while driving, as these could also indicate shock absorber problems.
If you notice any signs of wear or damage during the inspection, it is crucial to replace the shock absorbers promptly. While the exact lifespan of shock absorbers can vary depending on driving conditions and vehicle usage, it is generally recommended to replace them every 50,000 to 100,000 miles. However, it is essential to refer to the manufacturer’s recommendations and consult with a professional mechanic for guidance specific to your vehicle.