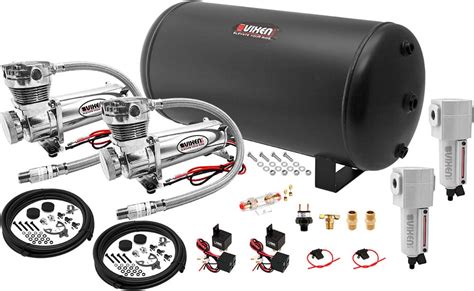
Truck air bag compressors play a crucial role in the suspension system of commercial vehicles. In this blog post, we will explore what a truck air bag compressor is, why it is important, and how it works. We will also discuss the different types of truck air bag compressors available and provide tips on choosing the right one for your vehicle. Additionally, we will delve into the installation process of a truck air bag compressor and offer maintenance tips to ensure its longevity. Finally, we will address common issues that may arise and highlight the benefits of using a truck air bag compressor.
What is a truck air bag compressor?
A truck air bag compressor is a vital component of a truck’s suspension system. It is responsible for inflating and deflating the air bags that support the truck’s load and provide a smooth ride. The compressor plays a crucial role in maintaining the proper air pressure in the air bags, ensuring that the truck remains stable and balanced on the road.
There are different types of truck air bag compressors available in the market. The most common ones are the single-path and dual-path compressors. Single-path compressors provide the same air pressure to both air bags, while dual-path compressors have separate channels to control the air pressure in each bag independently.
Installing a truck air bag compressor is a relatively straightforward process. It involves mounting the compressor and connecting it to the truck’s air suspension system. It is essential to follow the manufacturer’s instructions and ensure that all connections are secure to prevent any air leaks.
Why is a truck air bag compressor important?
A truck air bag compressor is an essential component of the truck’s air suspension system. It plays a crucial role in ensuring the proper functioning of the air bags, which are responsible for supporting the weight of the truck and providing a comfortable ride. Without a functional air bag compressor, the truck’s suspension system would not be able to maintain proper air pressure, resulting in a compromised ride quality and potential safety hazards.
One of the primary reasons why a truck air bag compressor is important is its role in maintaining the truck’s stability and balance. The air bags rely on a steady supply of compressed air to inflate and support the weight of the truck. Without a reliable compressor, the air bags would not be able to maintain the necessary air pressure, leading to an uneven distribution of weight and a destabilized truck. This can result in poor handling, increased tire wear, and decreased overall vehicle performance.
In addition to maintaining stability, a truck air bag compressor also contributes to the overall safety of the vehicle. By keeping the air bags properly inflated, it helps absorb the impact of bumps, potholes, and other road irregularities, providing a smoother and more controlled ride. This not only enhances the driver and passengers’ comfort but also reduces the risk of damage to the suspension system and other components of the truck. Furthermore, a properly functioning air bag compressor ensures that the air bags are always ready to deploy in the event of a sudden stop or collision, providing an additional layer of protection to the occupants of the truck.
- Improved stability and balance
- Enhanced ride quality
- Increased safety
Type | Advantages | Disadvantages |
---|---|---|
Single-path compressor | – Simpler design- Cost-effective | – Limited adjustability- May not be suitable for heavy payloads |
Dual-path compressor | – Greater adjustability- Better performance with heavy loads | – More complex system- Higher cost |
How does a truck air bag compressor work?
A truck air bag compressor is an important component of a truck’s air suspension system. It plays a crucial role in maintaining the proper pressure and inflation of the air bags. The air bags help to absorb shocks and provide a smoother ride, especially when carrying heavy loads. Understanding how a truck air bag compressor works is essential for truck owners and operators to ensure the optimal performance and longevity of their vehicles.
At its core, a truck air bag compressor is a device that pressurizes the air that is needed to inflate the air bags. It is typically powered by the vehicle’s engine or an independent motor. The compressor draws in air from the atmosphere and compresses it to a higher pressure. This pressurized air is then stored in a tank or reservoir until it is needed to inflate the air bags.
When the truck’s suspension system detects a change in load or an uneven surface, it sends a signal to the air bag compressor to release the stored air into the air bags. The air flows through a series of valves and hoses to reach the air bags, causing them to inflate and adjust accordingly. This inflation process helps to level the truck and improve its overall stability, especially when carrying heavy loads or traveling over rough terrain.
The truck air bag compressor also includes a pressure switch or sensor that monitors the pressure inside the air bags. If the pressure drops below the desired level, the compressor automatically kicks in to refill the air bags to the appropriate pressure. This continuous adjustment ensures that the air suspension system maintains optimal performance and provides a comfortable ride for the driver and passengers.
In conclusion, a truck air bag compressor is a vital component of a truck’s air suspension system. Its role is to pressurize and store the air that is needed to inflate the air bags, which helps to absorb shocks and provide a smoother ride. Understanding the inner workings of a truck air bag compressor is essential for truck owners and operators to ensure proper maintenance and functionality of their vehicles.
Different types of truck air bag compressors
A truck air bag compressor is an essential component of the air suspension system in trucks. It plays a crucial role in maintaining the correct air pressure within the air bags, which helps to support the weight of the truck and provide a smoother ride. Without a properly functioning compressor, the air bags would not be able to inflate or deflate as needed, leading to an imbalanced suspension system and a less comfortable driving experience.
There are several different types of truck air bag compressors available in the market. Each type has its own unique features and benefits. The most common types of truck air bag compressors include:
- Single-Level Compressors: These compressors have only one level of air pressure setting. They provide a fixed amount of air pressure to the air bags, which is suitable for trucks with a consistent payload or weight distribution.
- Dual-Level Compressors: These compressors offer two different levels of air pressure settings. This allows the driver to adjust the air pressure in the air bags according to the load they are carrying. Dual-level compressors are beneficial for trucks that frequently change their payload.
- Adjustable Compressors: As the name suggests, these compressors allow the driver to manually adjust the air pressure in the air bags. This gives the driver more control over the truck’s ride height and overall suspension performance.
Choosing the right truck air bag compressor depends on various factors such as the truck’s weight capacity, intended usage, and personal preferences. It is essential to consider these factors and consult with a professional before making a decision.
Maintaining the truck air bag compressor is also vital to ensure its longevity and proper functioning. Regular maintenance includes checking the compressor’s air filter, oil level, and overall condition. It is recommended to follow the manufacturer’s guidelines for maintenance and schedule periodic inspections to detect any issues early on.
In conclusion, truck air bag compressors come in different types to meet the specific needs of truck owners. Whether it is a single-level, dual-level, or adjustable compressor, each type offers its own set of advantages. Choosing the right compressor and properly maintaining it will contribute to better ride quality and overall performance of the truck’s air suspension system.
Choosing the right truck air bag compressor
Choosing the right truck air bag compressor is an important decision for any truck owner or operator. With so many options available on the market, it can be overwhelming to find the best compressor to suit your specific needs. However, by considering a few key factors, you can ensure that you select a compressor that is efficient, reliable, and compatible with your truck’s air bag system.
One of the first things to consider when choosing a truck air bag compressor is the size and capacity. Different trucks have different air bag systems, and it is crucial to select a compressor that can handle the specific requirements of your truck. The size and capacity of the compressor will determine how quickly and efficiently it can inflate the air bags, as well as how long it will take to recharge. Therefore, it is essential to match the compressor’s size to your truck’s air bag system.
Another factor to consider is the power source of the compressor. Some compressors are powered by the truck’s electrical system, while others may require a separate power source, such as a battery. It is important to determine which option is the most convenient and practical for your truck. Additionally, consider the power consumption of the compressor to ensure that it does not drain the truck’s battery excessively.
Furthermore, the durability and reliability of the truck air bag compressor should be taken into consideration. Look for a compressor that is made from high-quality materials, such as stainless steel or aluminum, to ensure its longevity. Additionally, read reviews and seek recommendations from other truck owners to ensure that the compressor you choose has a reputation for reliability and performance. After all, the last thing you want is for your air bag compressor to fail when you need it most.
In conclusion, choosing the right truck air bag compressor is essential for the safe and efficient operation of your truck’s air bag system. By considering factors such as size and capacity, power source, durability, and reliability, you can select a compressor that meets your specific needs. It is important to conduct thorough research and seek expert advice if necessary before making a decision. By investing in a high-quality compressor, you can have peace of mind knowing that your truck’s air bags are always ready to provide the necessary support and safety in case of an emergency.
Installation process of a truck air bag compressor
A truck air bag compressor is an essential component of air suspension systems in trucks. It helps to inflate and deflate the air bags, providing support and stability to the vehicle. The installation process of a truck air bag compressor involves several steps to ensure proper functioning and optimum performance. In this blog post, we will discuss the installation process of a truck air bag compressor, including the necessary tools and materials, as well as the step-by-step instructions to follow.
List of Required Tools and Materials:
- Truck air bag compressor kit
- Mounting brackets
- Solenoids
- Air hoses
- Fittings and connectors
- Wiring harness
- Relay and fuse
- Electrical connectors
- Wrenches and socket set
- Drill and drill bits
- Wire cutters and strippers
- Electrical tape and zip ties
Installation Process:
Step | Description |
---|---|
1 | Start by locating a suitable mounting location for the compressor. It should be in a clean and dry area, away from excessive heat, dirt, and moisture. |
2 | Using the mounting brackets and screws provided in the kit, securely attach the compressor to the chosen location. Ensure that it is mounted in a position that allows easy access for maintenance and servicing. |
3 | Next, install the solenoids near the air bags. These solenoids control the airflow to the air bags, allowing for inflation and deflation as needed. |
4 | Connect the air hoses to the compressor and the solenoids. Use the provided fittings and connectors to ensure a secure and leak-free connection. |
5 | Install the wiring harness, relay, and fuse. Connect the electrical wires to the compressor, solenoids, and battery. Use proper electrical connectors and ensure that all connections are tight and secure. |
6 | Check all connections and ensure that there are no loose or damaged parts. Secure any loose wires or hoses using zip ties or electrical tape. |
7 | Test the system by turning on the compressor and observing the inflation and deflation of the air bags. Make any necessary adjustments or repairs if needed. |
8 | Once the installation is complete and the system is functioning properly, double-check all connections and fasteners. Take the truck for a test drive to ensure that the air suspension system is working effectively. |
By following these step-by-step instructions, you can successfully install a truck air bag compressor and enhance the performance and stability of your truck’s air suspension system. Remember to refer to the manufacturer’s instructions and guidelines specific to your truck and compressor model for accurate installation.
Maintenance tips for truck air bag compressors
When it comes to maintaining truck air bag compressors, it’s essential to follow proper maintenance tips to ensure optimal performance and prolong their lifespan. Regular maintenance not only helps prevent potential breakdowns but also improves the overall safety of the vehicle. In this blog post, we will discuss some important maintenance tips for truck air bag compressors.
1. Check for leaks: Regularly inspect the air bag compressor and air lines for any leaks. Leaks can reduce the efficiency of the compressor and affect the functionality of the air bags. If you notice any leaks, promptly repair or replace the damaged parts.
2. Clean the compressor: Dust, debris, and dirt can accumulate in the compressor over time, affecting its performance. Regularly clean the compressor using compressed air or a soft brush to remove any buildup. Be cautious while cleaning to avoid damaging any sensitive components.
3. Monitor the air pressure: Keeping a close eye on the air pressure in the system is crucial for maintaining the proper functioning of the air bags. Use a pressure gauge to check the air pressure regularly and ensure it is within the recommended range. Adjust the pressure as needed to avoid over or under-inflation of the air bags.
4. Inspect electrical connections: The electrical connections of the truck air bag compressor should be inspected regularly to ensure they are secure and free from corrosion. Loose or corroded connections can lead to power failure and affect the performance of the compressor. Clean or tighten any loose connections and use appropriate corrosion protection.
5. Replace filters: Truck air bag compressors often have filters that help prevent dirt and debris from entering the system. Over time, these filters can become clogged, reducing the airflow and affecting the compressor’s efficiency. Regularly check and replace these filters according to the manufacturer’s recommendations.
By following these maintenance tips, you can ensure that your truck air bag compressor operates at its best and provides reliable performance. Regular maintenance not only enhances the longevity of the compressor but also contributes to the overall safety of your truck. Properly maintained air bag compressors can help prevent potential accidents and provide a smooth and comfortable ride.
Common issues with truck air bag compressors
A truck air bag compressor is an essential component of a truck’s air suspension system. It is responsible for pressurizing the air bags that support the weight of the vehicle. However, like any other mechanical device, truck air bag compressors can experience issues that may affect their performance. In this blog post, we will discuss some common issues that truck owners may encounter with their air bag compressors and how to address them.
One common issue with truck air bag compressors is inadequate pressure. If you notice that your truck is not sitting level or the air bags are not properly inflated, it could be due to insufficient pressure. This can be caused by a variety of factors, such as a faulty compressor motor, air leaks in the system, or a clogged air filter. To resolve this issue, you can start by checking the compressor’s motor and making sure it is running properly. If the motor is faulty, it may need to be repaired or replaced.
Another issue that truck owners may encounter is excessive noise coming from the air bag compressor. This can be a result of loose or worn-out components within the compressor. To address this issue, you can start by inspecting the compressor for any loose or damaged parts, such as bolts or brackets. Tightening or replacing these components can help reduce the noise. Additionally, it is important to regularly clean and lubricate the compressor to ensure smooth operation and prevent excessive wear and tear.
Finally, a common issue with truck air bag compressors is air leaks. Air leaks can occur in various parts of the system, such as the air lines, fittings, or even the air bags themselves. These leaks can lead to a loss of pressure and affect the overall performance of the air suspension system. To fix air leaks, it is important to carefully inspect the entire system for any signs of leaks, such as hissing sounds or visible cracks. Once the source of the leak is identified, you can repair or replace the affected component to ensure a proper seal and prevent further air loss.
- Check compressor motor for proper functioning
- Inspect and tighten loose or worn-out components
- Regularly clean and lubricate the compressor
- Inspect and repair any air leaks in the system
Issue | Cause | Solution |
---|---|---|
Inadequate pressure | Faulty compressor motor, air leaks, clogged air filter | Check motor, repair or replace if necessary |
Excessive noise | Loose or worn-out components | Inspect and tighten or replace components |
Air leaks | Leaks in air lines, fittings, or air bags | Identify and repair or replace affected components |
Overall, it is important to address any issues with truck air bag compressors promptly to ensure the proper functioning of the air suspension system. Regular maintenance and inspections can help identify and prevent potential problems, while prompt repairs can save you from costly repairs or replacements in the future. By understanding the common issues and their solutions, truck owners can enjoy a smooth and reliable air suspension system that enhances the comfort and stability of their vehicles.
Benefits of using a truck air bag compressor
A truck air bag compressor is an essential component of a vehicle’s air suspension system. It is responsible for supplying compressed air to the air bags, which then support the weight of the vehicle and provide a smooth and comfortable ride. The benefits of using a truck air bag compressor are numerous and can greatly enhance the performance, safety, and comfort of your truck.
One of the key benefits of using a truck air bag compressor is improved load carrying capacity. By adding air to the air bags, you can increase the load-carrying capacity of your truck. This is especially useful for individuals who frequently carry heavy loads or tow trailers. The ability to adjust the air pressure in the air bags allows for precise weight distribution and better control of the vehicle, reducing the risk of bottoming out or swaying.
Another advantage of using a truck air bag compressor is improved ride quality. The air bags absorb shocks and bumps on the road, providing a smoother and more comfortable ride. This is particularly beneficial for trucks that are often driven on rough terrains or uneven surfaces. The adjustable air pressure allows you to customize the ride height and stiffness according to your preferences, providing a personalized driving experience.
- Increased load carrying capacity
- Improved ride quality
- Enhanced vehicle stability and control
- Reduced tire wear
- Improved fuel efficiency
- Extended lifespan of suspension components
Benefit | Description |
---|---|
Increased load carrying capacity | The ability to adjust air pressure in the air bags allows for precise weight distribution and increased load carrying capacity. |
Improved ride quality | The air bags absorb shocks and bumps on the road, providing a smoother and more comfortable ride. |
Enhanced vehicle stability and control | By maintaining proper suspension height and adjusting air pressure, a truck air bag compressor improves vehicle stability and control, particularly when carrying heavy loads or towing. |
Reduced tire wear | The ability to adjust air pressure in the air bags helps distribute the weight evenly on the tires, reducing tire wear and improving overall tire life. |
Improved fuel efficiency | By optimizing the suspension system and reducing unnecessary weight, a truck air bag compressor can improve fuel efficiency. |
Extended lifespan of suspension components | The air bags absorb much of the impact and stress that would otherwise be placed on suspension components, resulting in a longer lifespan for these parts. |
In conclusion, the benefits of using a truck air bag compressor are significant and can greatly enhance the performance and comfort of your truck. Whether you need to increase load capacity, improve ride quality, enhance vehicle stability, reduce tire wear, improve fuel efficiency, or prolong the lifespan of suspension components, a truck air bag compressor is a valuable addition to your vehicle. Consider investing in a high-quality compressor to enjoy these benefits and make your truck even more versatile and reliable.
Frequently Asked Questions
What is a truck air bag compressor?
A truck air bag compressor is a device that is used to inflate and deflate air bags in a truck’s suspension system. It is responsible for maintaining the correct air pressure in the air bags to ensure proper support and stability.
Why is a truck air bag compressor important?
A truck air bag compressor is important because it helps in maintaining the proper ride height and balance of the truck. It enhances the overall performance and handling of the vehicle, improves load carrying capacity, and provides a comfortable ride for the driver and passengers.
How does a truck air bag compressor work?
A truck air bag compressor works by drawing in outside air and compressing it to a specific pressure level. This compressed air is then stored in the air bags, which are connected to the truck’s suspension system. The compressor can be manually or automatically controlled to inflate or deflate the air bags as required.
What are the different types of truck air bag compressors?
The different types of truck air bag compressors include portable compressors, on-board compressors, and electric compressors. Portable compressors are easily movable and can be connected to the truck’s battery for power. On-board compressors are permanently installed in the truck and are powered by the vehicle’s electrical system. Electric compressors, on the other hand, rely on an external power source for operation.
How do I choose the right truck air bag compressor?
When choosing a truck air bag compressor, it is important to consider factors such as load weight, truck model, and available space for installation. Additionally, the compressor’s duty cycle, CFM rating, and noise level should also be taken into account. It is recommended to consult a professional or refer to the truck’s manufacturer guidelines for selecting the appropriate compressor.
What is the installation process of a truck air bag compressor?
The installation process of a truck air bag compressor can vary depending on the specific compressor model and truck type. Generally, it involves mounting the compressor in a suitable location, connecting it to the truck’s battery and air bags, and installing any necessary piping and fittings. It is important to follow the manufacturer’s instructions and consult a professional if needed to ensure proper installation.
What are some maintenance tips for truck air bag compressors?
To maintain the optimal performance of a truck air bag compressor, regular maintenance is essential. This includes inspecting the compressor for any leaks, checking the air filter for cleanliness, and ensuring proper lubrication of moving parts. It is also important to follow the manufacturer’s recommended maintenance schedule and guidelines.
What are some common issues with truck air bag compressors?
Some common issues with truck air bag compressors include air leaks, compressor failure, and electrical problems. Air leaks can lead to a loss of pressure and improper functioning of the air bags. Compressor failure can result from excessive use, lack of maintenance, or component wear. Electrical issues can cause the compressor to malfunction or not operate at all.
What are the benefits of using a truck air bag compressor?
Benefits of using a truck air bag compressor include improved load carrying capacity, enhanced stability and control, reduced suspension fatigue, and a smoother ride. The compressor allows for easy adjustment of the air bag pressure to accommodate different loads, ensuring optimal performance and safety.