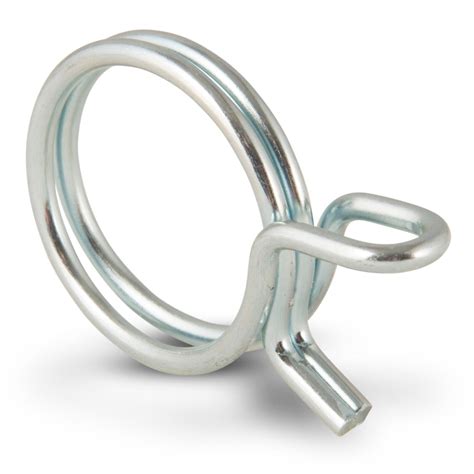
In the world of hoses and clamps, having the right equipment for the job is essential. Whether you’re a DIY enthusiast or a professional, understanding the different types of hoses, materials, sizes, and dimensions available is crucial for successful projects. In this blog post, we’ll delve into the world of hoses and clamps, exploring the various options and providing you with guidance on choosing, installing, troubleshooting, and maintaining them. From traditional clamps to quick-release systems and innovative hose technologies, we’ll cover it all. So, let’s get started on your journey to becoming a hose and clamp expert!
Types of Hoses for Different Applications
Hoses are an essential component in various applications, ranging from industrial to household use. However, not all hoses are created equal, and different applications require different types of hoses to ensure optimal performance. In this blog post, we will explore the different types of hoses and their specific applications, helping you choose the right hose for your needs.
1. Water Hoses: Water hoses are the most common type of hose used in households and gardens. They are designed to transport water from one point to another and are typically made of flexible rubber or PVC materials. Water hoses can be used for watering plants, washing cars, filling pools, and other general water-related tasks.
2. Air Hoses: Air hoses are designed to transport compressed air and are commonly used in pneumatic tools and equipment. They are typically made of reinforced PVC or rubber materials to withstand high-pressure air flow. Air hoses are essential in industries such as construction, automotive, and manufacturing.
3. Hydraulic Hoses: Hydraulic hoses are specifically designed to carry hydraulic fluid to power machinery and equipment. They are made of durable materials such as synthetic rubber or thermoplastic, reinforced with multiple layers to handle high-pressure hydraulic systems. Hydraulic hoses are widely used in industries like construction, agriculture, and mining.
- 4. Chemical Hoses: Chemical hoses are engineered to safely transport various chemicals, acids, and solvents. They are constructed with specific materials resistant to the chemicals they will come into contact with. Chemical hoses are crucial in industries such as chemical manufacturing, pharmaceuticals, and laboratories.
- 5. Food-Grade Hoses: Food-grade hoses are designed to meet strict hygienic standards for the transportation of food and beverages. These hoses are made of FDA-approved materials, ensuring that they won’t contaminate the food products they come into contact with. They are commonly used in food processing, catering, and beverage industries.
- 6. Vacuum Hoses: Vacuum hoses are used to create a suction force for various applications, including cleaning, material handling, and industrial processes. They are typically made of flexible PVC or rubber materials that can withstand negative pressures. Vacuum hoses are essential in industries such as janitorial services, woodworking, and dust collection systems.
It’s important to select the right type of hose for your specific application to ensure safety, efficiency, and durability. By understanding the different types of hoses available for different applications, you can make an informed decision and optimize your operations.
Type of Hose | Application |
---|---|
Water Hoses | Household and garden use, watering plants, washing cars, filling pools |
Air Hoses | Pneumatic tools, automotive, construction, manufacturing |
Hydraulic Hoses | Power machinery and equipment, construction, agriculture, mining |
Chemical Hoses | Chemical manufacturing, pharmaceuticals, laboratories |
Food-Grade Hoses | Food processing, catering, beverage industries |
Vacuum Hoses | Janitorial services, woodworking, dust collection systems |
By considering the specific requirements of your application and consulting with experts in the field, you can confidently choose the right hose type to meet your needs. Remember, using the appropriate hose ensures greater efficiency, safety, and longevity for your operations.
Choosing the Right Hose Material
When it comes to choosing the right hose material, it is important to consider the specific application and the conditions in which the hose will be used. Different materials offer varying levels of durability, flexibility, chemical resistance, and temperature tolerance. By understanding the properties of different hose materials, you can ensure that you select the most suitable option for your needs.
A commonly used hose material is PVC (Polyvinyl chloride), which is known for its affordability and versatility. PVC hoses are lightweight, flexible, and resistant to abrasion, making them suitable for a wide range of applications such as irrigation, gardening, and general water transportation. However, PVC hoses may not be suitable for use with certain chemicals or in high-temperature environments.
For applications that involve the transfer of chemicals or fluids, it is important to choose a hose material that is chemically resistant. One such material is Teflon (PTFE), which offers excellent resistance to a wide range of chemicals and solvents. Teflon hoses are commonly used in industries such as chemical processing, pharmaceuticals, and food processing. They can withstand high temperatures and offer low friction, making them ideal for applications where cleanliness and purity are important.
- Nitrile (NBR) hoses are known for their oil resistance, making them suitable for applications in the automotive industry, oil and gas industry, and fuel transfer.
- EPDM (Ethylene Propylene Diene Monomer) hoses are resistant to ozone, weather, and UV rays, making them ideal for outdoor applications such as gardening and irrigation.
- Silicone hoses are known for their high temperature resistance and are commonly used in industries such as automotive, aerospace, and medical.
Hose Material | Advantages | Disadvantages |
---|---|---|
PVC | Affordable, versatile, lightweight | Not suitable for certain chemicals, limited temperature range |
Teflon (PTFE) | Chemically resistant, high temperature tolerance, low friction | Relatively expensive |
Nitrile (NBR) | Oil resistance | May not be suitable for other chemicals or fluids |
EPDM | Ozone and weather resistance, UV resistant | Limited temperature range |
Silicone | High temperature resistance | Relatively expensive |
These are just a few examples of hose materials and their advantages and disadvantages. It is important to thoroughly research and consider the requirements of your specific application before making a decision. Some factors to consider include the type of fluid or chemical being transferred, the temperature range, pressure requirements, and any specific industry regulations or standards that must be met.
In conclusion, choosing the right hose material is crucial for ensuring optimal performance and durability in various applications. By understanding the properties of different materials and considering the specific requirements of your application, you can make an informed decision and select a hose material that will meet your needs effectively.
Understanding Various Hose Sizes and Dimensions
Hoses come in various sizes and dimensions, and it’s important to understand these specifications to ensure you choose the right hose for your application. The size and dimensions of a hose not only determine its compatibility with fittings and connectors but also affect its flow rate and overall performance. In this blog post, we will explore the different aspects of hose sizes and dimensions and how they play a crucial role in various industries.
When it comes to hose sizes, the most common measurement used is the inner diameter (ID). The ID determines the flow capacity of the hose, as it directly relates to the volume of fluid that can pass through. Hoses with larger inner diameters can handle higher flow rates, making them suitable for applications where swift fluid transfer is needed. Conversely, hoses with smaller inner diameters are ideal for applications that require precise flow control or limited fluid volumes.
Aside from the inner diameter, another crucial dimension to consider is the outer diameter (OD) of the hose. The OD affects compatibility with fittings and connectors, as well as the overall flexibility and durability of the hose. When selecting a hose, it’s important to ensure that the OD matches the requirements of the connectors and fittings you plan to use. Additionally, hoses with larger ODs tend to have thicker walls, providing enhanced strength and resistance to external wear and tear.
It’s also worth noting that hose dimensions can vary based on the material composition. For instance, hoses made from different materials, such as rubber, PVC, or silicone, may have varying thicknesses and tolerances. Additionally, specific industries may have their own standardized hose sizes and dimensions to meet unique requirements. Therefore, it’s essential to consult industry guidelines and standards to ensure compliance and optimal performance.
In summary, understanding various hose sizes and dimensions is crucial for selecting the right hose for your specific application. Factors such as inner diameter, outer diameter, and material composition all play important roles in determining the hose’s flow capacity, compatibility, flexibility, and durability. By considering these factors and consulting industry guidelines, you can make informed decisions when choosing hoses that meet your needs and provide efficient fluid transfer in different environments.
Common Hose Clamps and Their Uses
When it comes to hoses, one important component that often goes unnoticed is the hose clamp. These simple yet vital tools play a crucial role in ensuring that hoses stay securely connected to their fittings, preventing leaks and potential damage. In this blog post, we will explore the different types of hose clamps available and their specific uses.
List of Common Hose Clamps:
Clamp Type | Uses |
---|---|
Screw/Band Clamps | Used for a wide range of applications, including automotive, plumbing, and irrigation systems. |
Spring Clamps | Often used for low-pressure applications and can be easily installed without any special tools. |
Wire Clamps | Ideal for high-pressure applications and provide a strong and reliable connection. |
T-Bolt Clamps | Designed for heavy-duty applications and commonly used in automotive and industrial settings. |
Each type of hose clamp has its own advantages and is suitable for different situations. Screw/band clamps, also known as worm clamps, are the most common type and can be easily adjusted to fit various hose sizes. Spring clamps, on the other hand, are more convenient for quick and temporary connections. Wire clamps provide a secure connection that can withstand high pressure, making them perfect for industrial applications. T-bolt clamps are best suited for heavy-duty applications where a strong and reliable connection is required.
Troubleshooting Common Hose and Clamp Problems:
In addition to understanding the different types of hose clamps, it is essential to be aware of common problems that can arise. Some of these issues include leaks, loose connections, and improper installation. To troubleshoot these problems, always check for any visible signs of wear or damage on the hoses and clamps. Tighten or replace loose or damaged clamps, and ensure that the hoses are properly seated on the fittings. Regular inspections and maintenance can help prevent potential issues and ensure the reliable performance of hoses and clamps.
As we have seen, hose clamps are a crucial component in various applications and play a significant role in securing hoses. By understanding the different types of clamps and their specific uses, as well as troubleshooting common problems, you can ensure the proper functioning and longevity of your hoses.
Step-by-Step Guide to Properly Installing Hose Clamps
When it comes to proper installation of hose clamps, following a step-by-step guide is essential to ensure a secure and leak-free connection. Hose clamps are commonly used to secure hoses onto fittings or other components, preventing leaks and maintaining the integrity of the system. By understanding the correct installation process, you can avoid common problems such as hose slippage or damage to the clamp itself.
Step 1: Choose the Right Clamp Size
Before starting the installation process, it is important to select the correct size of hose clamp. The size of the clamp should correspond to the outer diameter of the hose being used. Using a clamp that is too small can result in insufficient sealing, while using a clamp that is too large may not provide adequate tightening. Refer to the manufacturer’s guidelines or consult a professional if you are unsure about the appropriate clamp size for your specific application.
Step 2: Prepare the Hose
Prior to installing the hose clamp, make sure the hose is properly prepared. This includes removing any dirt, debris or old fittings from the hose end. Additionally, ensure that the end of the hose is cut cleanly and evenly, without any frayed edges or irregularities. Any irregularities or rough edges can affect the sealing capability of the clamp.
Step 3: Position the Clamp
Position the clamp over the hose, near the fitting or component that it will be secured to. Ensure that the clamp is centered and aligned properly, allowing for equal tightening on all sides. The screw or band of the clamp should face outwards, making it accessible for tightening.
Step 4: Tighten the Clamp
To tighten the hose clamp, use a suitable tool such as a screwdriver or a hose clamp plier. Gradually tighten the clamp by turning the screw or tightening the band, starting from the furthest point from the fitting. Avoid over-tightening the clamp, as this can cause damage to the hose or the fitting. Check for any resistance or bulging of the hose during the tightening process, as this may indicate that the clamp is too tight.
Step 5: Verify the Sealing
After tightening the clamp, verify the sealing by conducting a visual inspection. Ensure that the clamp is securely holding the hose in place without any gaps or slippage. Additionally, check for any signs of leakage or seepage around the connection. If any issues are detected, reposition or retighten the clamp as needed to achieve a proper seal.
By following these step-by-step instructions, you can ensure a successful and proper installation of hose clamps. Remember to choose the right clamp size, prepare the hose properly, position the clamp correctly, tighten it gradually, and check for proper sealing. Proper installation will not only prevent leaks but also enhance the longevity and efficiency of your hose system.
Troubleshooting Common Hose and Clamp Problems
Hoses and clamps are essential components in various applications, ranging from industrial settings to household chores. However, like any other mechanical system, they can encounter problems that require troubleshooting. In this blog post, we will explore some common hose and clamp problems that you may encounter and provide solutions to help you resolve them quickly and efficiently.
Leakage: One of the most common issues with hoses is leakage. Whether it’s a small drip or a major leak, it can disrupt the functioning of the system and cause damage. The first step in troubleshooting leakage is to identify the source of the problem. It could be a loose connection, a worn-out hose, or a faulty clamp. Tightening the connections or replacing the hose may solve the issue. Additionally, using hose clamps that provide a secure and tight fit can prevent leakage.
Cracks and Tears: Hoses are subjected to a lot of stress and wear over time, which can result in cracks or tears. This can occur due to excessive pressure, exposure to harsh chemicals, or improper handling. When troubleshooting cracks and tears, careful inspection is crucial. Look for any visible signs of damage and replace the hose if necessary. It is also essential to choose the right hose material that withstands the specific application requirements to avoid such problems.
Corrosion and Rust: Another common issue that can affect hoses and clamps is corrosion and rust. This occurs when the fittings and clamps come in contact with moisture, chemicals, or substances that promote oxidation. Regular maintenance and inspection can help identify early signs of corrosion, enabling timely troubleshooting. Applying a protective coating or using corrosion-resistant materials for clamps and fittings can help prevent this problem.
- Inadequate Seal: An inadequate seal between the hose and the connection point can lead to air or fluid leaks. This can be caused by a worn-out or damaged clamp. Troubleshooting this issue involves checking the clamp for any signs of wear or deformation. If the clamp is damaged, replacing it with a new one should solve the problem. Additionally, ensuring that the clamp is properly tightened can help create a tight seal and prevent leakage.
- Clamp Slippage: Sometimes, clamps may slip or become loose over time. This can result in an unstable connection, leading to leakage or inefficient system performance. Troubleshooting clamp slippage requires tightening the clamp securely. If the problem persists, using a different type of clamp or opting for quick-release clamps can provide a more reliable and secure connection.
Problem | Probable Cause | Troubleshooting |
---|---|---|
Leakage | Loose connections or worn-out hose | Tighten connections or replace hose |
Cracks and Tears | Excessive pressure or exposure to harsh chemicals | Inspect for damage and replace hose if necessary |
Corrosion and Rust | Moisture or exposure to chemicals | Apply protective coating or use corrosion-resistant materials |
Troubleshooting common hose and clamp problems is crucial to ensure the efficient functioning and longevity of your system. Regular inspection, choosing the right materials, and proper maintenance can help prevent these issues from occurring in the first place. By addressing these problems promptly, you can avoid costly repairs and ensure the smooth operation of your hoses and clamps.
Maintenance Tips for Extending the Lifespan of Hoses and Clamps
Regular maintenance is key to ensuring the longevity and efficient functioning of hoses and clamps. By following a few simple tips, you can extend the lifespan of these essential components and avoid costly repairs or replacements.
1. **Inspecting for Damage**: Regularly inspecting hoses and clamps for any signs of wear and tear is crucial. Look out for cracks, leaks, bulges, or any other visible damage. Identifying issues early on can prevent further damage and potential system failures.
2. **Cleaning and Lubricating**: Keep hoses and clamps clean by removing any dirt, debris, or residue. Make sure to use appropriate cleaning agents that are compatible with the material of the hoses. Additionally, lubricating the joints and connections can help reduce friction and enhance the overall performance.
3. **Proper Storage**: When not in use, hoses and clamps should be properly stored to prevent damage. Avoid exposing them to extreme temperatures or direct sunlight. Coiling hoses and securing them with appropriate clamps can help maintain their shape and prevent kinks or twists.
4. **Avoid Overstretching**: Hoses should not be stretched beyond their maximum capacity. Overstretching can weaken the material and lead to leaks or bursts. Make sure to use hoses that are suitable for the intended application and adhere to the recommended pressure ratings.
5. **Regular Replacement**: Despite proper maintenance, hoses and clamps will eventually wear out over time. It is important to establish a regular replacement schedule based on the manufacturer’s guidelines and the specific usage conditions. This will help prevent unexpected failures and ensure the safety of your system.
By following these maintenance tips, you can significantly prolong the lifespan of your hoses and clamps. Regular inspections, proper cleaning, and storage practices will not only save you money in the long run but also contribute to the smooth operation of your equipment and systems.
Comparing Traditional Clamps vs. Quick-Release Clamps
When it comes to securing hoses and ensuring proper fluid flow, the type of clamp used is of utmost importance. In the world of clamps, two main options are commonly used: traditional clamps and quick-release clamps. While both types serve the same purpose, there are significant differences between them that may impact your choice. Let’s take a closer look at the advantages and disadvantages of each type to help you make an informed decision.
Traditional Clamps:
A traditional clamp, also known as a worm drive clamp or screw clamp, consists of a band with a screw mechanism. These clamps are typically made of stainless steel or galvanized steel, offering excellent durability and resistance to corrosion. One of the main advantages of traditional clamps is their ability to provide a strong and secure hold. The screw mechanism allows for precise tension adjustment, ensuring a tight grip on the hose. Additionally, traditional clamps are readily available and cost-effective, making them a popular choice in various industries.
However, there are a few drawbacks to consider when using traditional clamps. Firstly, they require the use of tools, such as a screwdriver, to tighten or loosen the clamp. This can be time-consuming, especially when dealing with multiple clamps. Additionally, if over-tightened, traditional clamps can damage the hose by cutting into the material or causing deformation. Therefore, caution must be exercised during installation to avoid such issues.
Quick-Release Clamps:
Quick-release clamps, also known as spring clamps or T-bolt clamps, offer a more convenient and efficient alternative to traditional clamps. These clamps consist of a band with a spring-loaded mechanism, allowing for quick and easy installation or removal. The spring-loaded design enables rapid adjustment and provides constant tension on the hose, ensuring a secure connection. Quick-release clamps are often made of stainless steel or nylon, offering good resistance to corrosion and durability.
The main advantage of quick-release clamps is their simplicity and speed of use. Unlike traditional clamps, they do not require any tools for installation or removal, saving time and effort. Moreover, quick-release clamps distribute pressure more evenly along the hose, reducing the risk of damage. This type of clamp is especially useful in applications where frequent hose assembly/disassembly is required.
However, quick-release clamps are typically more expensive than traditional clamps. Additionally, they may not provide the same level of clamping force as traditional clamps, which may be a consideration in high-pressure applications. It is also important to note that quick-release clamps have size limitations, and the available sizes may not be as extensive as traditional clamps.
Traditional Clamps | Quick-Release Clamps |
---|---|
Require tools for installation or removal | No tools required for installation or removal |
Possible risk of over-tightening and damaging the hose | Even pressure distribution reduces the risk of hose damage |
Cost-effective | Relatively more expensive |
Extensive range of sizes available | Size limitations |
In conclusion, when comparing traditional clamps to quick-release clamps, it’s crucial to consider your specific application requirements. Traditional clamps offer a strong hold and cost-effectiveness but require tools and careful installation. On the other hand, quick-release clamps provide convenience and ease of use but may be pricier and have size limitations. By assessing the advantages and disadvantages of each type, you can choose the clamp that best suits your needs and ensures the optimal performance of your hoses.
Exploring Innovative Hose Technologies and Clamping Systems
When it comes to hoses and clamping systems, there have been significant advancements in technology in recent years. These innovative solutions have revolutionized various industries and applications, providing improved performance, durability, and ease of use. In this blog post, we will explore some of the most exciting hose technologies and clamping systems available in the market today.
1. Quick-Release Clamps: Quick-release clamps are designed to provide efficient and effortless installation and removal of hoses. These clamps feature a unique mechanism that allows for quick adjustment and secure fastening. With their user-friendly design, quick-release clamps eliminate the need for specialized tools and significantly reduce installation time.
2. High-Pressure Hose Technologies: With the growing demand for higher pressure applications, hose manufacturers have developed advanced technologies to meet these requirements. High-pressure hoses are specifically designed to withstand extreme pressure levels, ensuring safe and reliable performance. These hoses are constructed using reinforced materials and robust manufacturing techniques to deliver exceptional strength and durability.
3. Composite Hose Systems: Composite hoses are becoming increasingly popular for their versatile applications and superior performance. These hoses are constructed with multiple layers of different materials, such as thermoplastics, fabrics, and metals, to provide a combination of properties. Composite hoses offer excellent chemical resistance, flexibility, and durability, making them ideal for challenging environments and corrosive applications.
Hose Technology/Clamping System | Key Features |
---|---|
Quick-Release Clamps | Efficient installation and removalQuick adjustment and secure fasteningEliminates need for specialized tools |
High-Pressure Hose Technologies | Designed for extreme pressure applicationsExceptional strength and durability |
Composite Hose Systems | Versatile applicationsChemical resistanceFlexibility and durability for challenging environments |
These innovative hose technologies and clamping systems offer a range of benefits to various industries. From easy installation and removal to enhanced performance and reliability, these advancements have improved efficiency and safety in countless applications. Whether it is the quick-release clamps for fast and secure hose connections or the composite hose systems for challenging environments, businesses now have access to cutting-edge solutions for their specific needs.
As technology continues to evolve, we can expect even more innovative hose technologies and clamping systems in the future. These advancements will undoubtedly further improve efficiency, durability, and safety, giving industries the tools they need to meet the evolving demands of their applications. Stay updated with the latest developments in the hose and clamping industry to benefit from these advancements and make informed decisions for your business.
Frequently Asked Questions
Q: What types of hoses are available for different applications?
A: There are various types of hoses available, such as garden hoses, fuel hoses, air hoses, hydraulic hoses, and suction hoses. Each type is designed to meet specific application requirements.
Q: How do I choose the right hose material?
A: The choice of hose material depends on factors like the type of fluid or gas being conveyed, temperature and pressure conditions, and compatibility with chemicals or substances. Common hose materials include rubber, PVC, polyurethane, and stainless steel.
Q: How do I understand various hose sizes and dimensions?
A: Hose sizes are typically measured based on the inner diameter (ID) or outer diameter (OD) of the hose. It is important to refer to the manufacturer’s specifications to determine the appropriate hose size for your specific application.
Q: What are common hose clamps and their uses?
A: Common hose clamps include worm gear clamps, T-bolt clamps, spring clamps, and constant tension clamps. They are used to secure hoses onto fittings or connections, providing a tight and leak-proof seal.
Q: How do I properly install hose clamps?
A: To properly install hose clamps, ensure the clamp is the correct size for the hose and fitting. Position the clamp over the hose and tighten it using a screwdriver or appropriate tool until secure. Avoid overtightening, as it may damage the hose or fitting.
Q: What are some troubleshooting tips for common hose and clamp problems?
A: Common hose and clamp problems include leaks, cracks, kinks, and loose connections. Troubleshooting tips include checking for proper installation, inspecting for damage or wear, replacing worn-out clamps or hoses, and ensuring the correct hose size and material are used.
Q: How can I extend the lifespan of hoses and clamps through maintenance?
A: Regular maintenance includes inspecting hoses and clamps for damage, cleaning them, storing them properly when not in use, and avoiding exposure to excessive heat, chemicals, or sunlight. Adequate maintenance can help extend the lifespan of hoses and clamps.
Q: What are the differences between traditional clamps and quick-release clamps?
A: Traditional clamps require tools for installation and removal, while quick-release clamps have a mechanism that allows for easy and fast installation or removal without the need for tools. Quick-release clamps are convenient for applications that require frequent hose assembly/disassembly.
Q: What are some innovative hose technologies and clamping systems available?
A: Some innovative hose technologies and clamping systems include push-to-connect fittings, crimped fittings, self-retracting reels, and smart hose technologies. These advancements enhance efficiency, ease of use, and reliability in various applications.