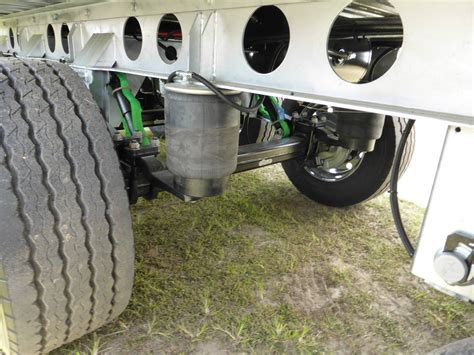
When it comes to heavy truck applications, air spring durability is of utmost importance. Understanding the significance of air spring durability is crucial for truck owners and operators to ensure optimal performance and longevity of their vehicles. In this blog post, we will explore the various factors that affect the durability of air springs, the role of material selection in enhancing their lifespan, and the impact of heavy truck loads. Additionally, we will discuss maintenance practices, signs of wear and potential failure, and strategies for extending the lifespan of air springs. Furthermore, we will delve into the importance of proper installation and selecting the right air springs for heavy truck applications through case studies of successful strategies. Join us as we explore the realm of air spring durability and discover how to maximize the performance and reliability of your heavy truck.
Understanding the Importance of Air Spring Durability
The durability of air springs is a crucial factor to consider when it comes to heavy truck applications. Air springs are commonly used in heavy-duty trucks for a variety of reasons, including their ability to provide a smooth ride and improve vehicle stability. However, if not properly maintained and cared for, air springs can wear out quickly, leading to potential failures and safety hazards. Understanding the importance of air spring durability is essential for truck owners and operators.
One of the key factors that affect the durability of air springs is the choice of materials used in their construction. Air springs are typically made of rubber or synthetic materials that are resistant to wear and tear. The quality and composition of these materials play a significant role in determining how long the air springs will last. It is essential to choose air springs that are manufactured using high-quality materials to ensure their durability and longevity.
Another factor that can impact the durability of air springs is the weight and load they are subjected to. Heavy truck loads can put immense pressure on the air springs, causing them to wear out faster. It is crucial to consider the weight capacity and load rating of the air springs when selecting the appropriate ones for a specific truck application. Choosing air springs that can handle heavy loads will help prevent premature wear and ensure their durability.
Maintaining proper maintenance practices is imperative for enhancing the durability of air springs. Regular inspections, lubrication, and cleaning can help identify any signs of wear or potential failures early on. Prompt repairs or replacements can be made to avoid any further damage and extend the lifespan of the air springs. Additionally, following manufacturer guidelines and recommendations regarding installation and maintenance procedures can significantly contribute to the durability of air springs.
To better understand the importance of air spring durability, let’s look at some case studies where successful strategies were implemented to enhance their durability. These case studies provide valuable insights into the best practices and techniques that can be used to improve the lifespan of air springs. By learning from real-life examples, truck owners and operators can gain knowledge and expertise in maintaining and maximizing the durability of their air springs.
In conclusion, understanding the importance of air spring durability is crucial for heavy truck owners and operators. Factors such as material selection, heavy truck loads, maintenance practices, and learning from case studies all play a significant role in enhancing the durability of air springs. By recognizing these factors and implementing appropriate strategies, truck owners can ensure the longevity and reliability of their air springs, resulting in improved vehicle performance, safety, and cost-effectiveness.
Factors Affecting the Durability of Air Springs
When it comes to air springs, durability is a crucial factor to consider. Air springs, also known as air suspension systems, play a vital role in providing a smooth and comfortable ride for heavy trucks and vehicles. However, they are exposed to various factors that can affect their overall durability. Understanding the factors that impact air spring durability is essential for ensuring their longevity and efficient performance.
Maintenance: Regular and proper maintenance plays a significant role in enhancing the durability of air springs. This includes inspecting the air springs for signs of wear and tear, checking the air pressure, and ensuring proper lubrication. Routine maintenance can help identify potential issues early on and prevent further damage, ultimately extending the lifespan of the air springs.
Material Selection: The choice of materials used in manufacturing air springs greatly affects their durability. High-quality materials, such as durable rubber compounds and reinforced fabrics, ensure that the air springs can withstand heavy loads, extreme temperatures, and various road conditions. The use of inferior materials can result in premature wear and failure of the air springs.
Operating Conditions: The operating conditions under which air springs are subjected to also impact their durability. Factors such as the weight of the load carried, frequency of use, rough terrains, and extreme weather conditions can put significant stress on the air springs. Overloading the air springs or subjecting them to harsh conditions can lead to accelerated wear and tear, reducing their durability.
To summarize, several factors influence the durability of air springs. Proper maintenance practices, careful material selection, and considering the operating conditions are vital to ensure the longevity and efficient performance of air springs. By understanding these factors and taking necessary precautions, it is possible to extend the lifespan of air springs and avoid potential failures and costly replacements.
The Role of Material Selection in Air Spring Durability
When it comes to air spring durability, one of the key factors that plays a crucial role is the selection of materials used in their construction. The right choice of materials can significantly enhance the lifespan and performance of air springs, ensuring their long-lasting functionality in heavy truck applications.
Firstly, quality materials contribute to the overall strength and resilience of air springs. They need to withstand the constant pressure and load exerted on them, as well as the frequent compression and expansion cycles. Materials like high-quality rubber blends, reinforced with durable fibers such as polyester or nylon, are commonly used in the construction of air springs. These materials offer exceptional resistance to wear and tear, ensuring the springs can endure the demanding conditions they are exposed to.
Secondly, the specific application requirements should be taken into account when selecting the materials for air springs. Different trucks and vehicles have varying load capacities, operating conditions, and environmental factors that may impact the durability of air springs. For instance, air springs used in off-road or construction vehicles may need to be made from materials that offer superior resistance to abrasion, extreme temperatures, or chemicals. In contrast, air springs used in standard heavy-duty trucks may require different properties. Therefore, material selection should be based on a careful analysis of the application’s demands to ensure optimal performance and longevity of the air springs.
Lastly, ongoing research and development in material science plays a critical role in enhancing air spring durability. Manufacturers strive to improve their products by experimenting with new materials and technologies. For example, advancements in elastomeric blends have enabled the development of innovative materials that offer higher load capacity, better resistance to fatigue, and improved overall durability. Manufacturers also conduct extensive testing and analysis to ensure that the selected materials meet the required industry standards and specifications for air springs.
- In conclusion, the role of material selection in air spring durability cannot be overstated. High-quality and appropriate materials are essential for ensuring the longevity and reliable performance of air springs in heavy truck applications.
- The selection of materials that can withstand the continuous load, pressure, and environmental conditions is crucial to prevent premature wear and potential failure of air springs.
- Manufacturers continue to invest in research and development to explore new materials and technologies that can further enhance the durability and overall performance of air springs in various heavy truck applications.
Impact of Heavy Truck Loads on Air Spring Durability
Heavy truck loads can have a significant impact on the durability of air springs. As these trucks carry large amounts of weight, the air springs are subject to extreme pressure and stress. It is crucial to understand the effects of heavy truck loads on air spring durability to ensure the proper functioning and longevity of these essential components.
One of the main factors that affect the durability of air springs under heavy truck loads is the weight distribution. When a truck is overloaded or the weight is unevenly distributed, it puts excessive strain on the air springs. This can lead to premature wear and tear, reducing their lifespan.
In addition to weight distribution, the frequency and duration of heavy truck loads also play a role in air spring durability. If a truck frequently carries heavy loads or operates for prolonged periods while overloaded, the air springs are more likely to experience fatigue and failure.
Factors Affecting the Durability of Air Springs:
- Weight Distribution: Proper weight distribution is crucial to prevent excessive strain on air springs.
- Frequency and Duration of Heavy Loads: Frequent or prolonged heavy loads can lead to fatigue and failure of air springs.
Factors | Effects |
---|---|
Weight Distribution | Uneven weight distribution puts excessive strain on air springs, reducing their durability. |
Frequency and Duration of Heavy Loads | Frequent or prolonged heavy loads can lead to fatigue and failure of air springs. |
To mitigate the impact of heavy truck loads on air spring durability, proper maintenance and regular inspections are essential. It is crucial to check for signs of wear and potential failure, such as cracks, leaks, or uneven wear on the air springs. Prompt replacement of worn-out or damaged air springs is necessary to prevent further damage to the suspension system and ensure the truck’s safe operation.
Furthermore, choosing high-quality air springs that are specifically designed for heavy truck applications is crucial. These air springs are engineered to withstand the increased stress and pressure associated with heavy loads, enhancing their durability and performance.
In conclusion, the impact of heavy truck loads on air spring durability cannot be ignored. Proper weight distribution, careful selection of air springs, and regular maintenance practices are essential to ensure the longevity and optimal performance of these vital components. By taking these factors into consideration, heavy truck owners and operators can extend the lifespan of their air springs and minimize the risk of potential failures and costly repairs.
Maintenance Practices to Enhance Air Spring Durability
Maintenance Practices to Enhance Air Spring Durability
Proper maintenance practices play a crucial role in extending the lifespan and enhancing the durability of air springs. These components are essential in providing a smooth and comfortable ride for heavy trucks and commercial vehicles. By implementing regular maintenance routines, operators can significantly reduce the risk of premature wear and potential failure of their air springs.
One of the most important maintenance practices is regular inspections. Operators should visually inspect the air springs for any signs of wear, damage, or potential issues. This includes checking for cracks, leaks, or abrasions on the rubber bellows and metal parts of the air spring. Inspecting the mounting brackets and hardware for any looseness or corrosion is also crucial. By identifying and addressing potential issues early on, operators can prevent further damage and ensure the optimal functioning of their air springs.
In addition to inspections, another important maintenance practice is proper inflation and pressure management. Air springs rely on compressed air to support the weight of the vehicle and provide suspension. It is essential to maintain the correct air pressure within the recommended range specified by the manufacturer. Underinflated air springs can lead to excessive stress on the components, resulting in premature wear and reduced durability. On the other hand, overinflated air springs can cause a harsher ride, as well as increase the risk of damage due to excessive pressure. Regularly monitoring and adjusting the air pressure based on the vehicle’s load and operating conditions is crucial for maintaining optimal air spring durability.
Furthermore, proper lubrication is vital to enhance the durability of air springs. Lubricating the metal components of the air spring, such as the piston rod and mounting brackets, helps reduce friction and wear. Operators should use the recommended lubricants specified by the manufacturer and follow the recommended lubrication intervals. Additionally, any grease or dirt buildup should be cleaned regularly to prevent corrosion and ensure smooth operation.
Implementing these maintenance practices, such as regular inspections, proper inflation and pressure management, and adequate lubrication, can significantly enhance the durability of air springs. By taking proactive measures to maintain these vital components, operators can maximize the lifespan of their air springs and minimize the risk of downtime, potential failures, and costly repairs.
Signs of Air Spring Wear and Potential Failure
Air springs are an integral component of heavy truck suspension systems, providing support and cushioning to ensure a smooth ride. However, like any mechanical part, air springs can wear out over time and fail, leading to potential safety hazards and costly repairs. It is crucial for truck owners and operators to be aware of the signs of air spring wear and potential failure, as early detection can help prevent accidents and minimize downtime.
One of the most common signs of air spring wear is a noticeable decrease in ride comfort. As the air spring deteriorates, it may not be able to effectively absorb shocks and vibrations, resulting in a rough and bumpy ride. This can be particularly evident when driving over uneven surfaces or encountering obstacles on the road. Additionally, the truck may experience excessive bouncing or swaying, indicating that the air spring’s damping capabilities have been compromised.
Another telltale sign of air spring wear is air leakage. If you notice a persistent hissing or whistling noise coming from the suspension system, it could indicate a leak in the air spring assembly. This leakage may be caused by a puncture or damage to the air spring’s rubber bladder or seals. It is essential to address air leaks promptly, as they can lead to loss of air pressure and a subsequent loss of suspension support, potentially resulting in a dangerous driving condition.
In addition to decreased ride comfort and air leakage, visual inspection can also reveal signs of air spring wear. Examine the air spring for any cracks, abrasions, or bulges on the rubber bladder. These physical damages can occur due to prolonged exposure to harsh road conditions, extreme temperatures, or overloading of the truck. Any visible signs of wear indicate that the air spring’s structural integrity has been compromised, making it more susceptible to failure.
- Decreased ride comfort
- Excessive bouncing or swaying
- Air leakage
- Cracks, abrasions, or bulges on the rubber bladder
Signs of Air Spring Wear | Potential Failure |
---|---|
Decreased ride comfort | Loss of suspension support, rough and bumpy ride |
Excessive bouncing or swaying | Reduced stability, compromised handling |
Air leakage | Loss of air pressure, dangerous driving condition |
Cracks, abrasions, or bulges on the rubber bladder | Structural integrity compromised, potential rupture |
In conclusion, recognizing the signs of air spring wear and potential failure is crucial for maintaining the safety and performance of heavy trucks. Regular inspection, both visually and audibly, can help identify early warning signs such as decreased ride comfort, excessive bouncing, air leakage, and visible structural damage. If any of these signs are detected, it is essential to consult with a professional for appropriate repairs or replacements. By addressing these issues promptly, truck owners can ensure the longevity and reliability of their air suspension systems, minimizing the risk of costly breakdowns and accidents on the road.
Extending the Lifespan of Air Springs through Proper Installation
Proper installation plays a crucial role in enhancing the lifespan of air springs. Whether it is for heavy truck applications or other industrial uses, ensuring that air springs are installed correctly can significantly improve their durability and performance. Improper installation can lead to premature wear and potential failure of air springs, resulting in costly repairs and downtime. In this blog post, we will discuss some important tips and best practices for installing air springs to maximize their longevity.
1. Follow the Manufacturer’s Guidelines:
When installing air springs, it is essential to carefully read and follow the manufacturer’s guidelines and instructions. Manufacturers provide specific recommendations for installation procedures, torque specifications, and any additional steps that may be required. Following these guidelines will ensure that the air springs are installed correctly and in accordance with the manufacturer’s specifications.
2. Use Proper Tools and Equipment:
Using the right tools and equipment is crucial for a successful air spring installation. Make sure to have the necessary tools and equipment on hand, such as torque wrenches, air suspension jacks, and safety equipment. Using improper tools or equipment can lead to incorrect installation, which may result in damage to the air springs or their components.
3. Inspect and Prepare the Mounting Surface:
Prior to installation, it is important to inspect and prepare the mounting surface for the air springs. The mounting surface should be clean, free from any debris, and in good condition. Any surface irregularities or damage can affect the proper functioning of the air springs and reduce their lifespan. Additionally, ensure that the mounting surface is properly aligned to prevent any unnecessary stress on the air springs.
4. Check for Proper Alignment and Clearance:
During the installation process, it is crucial to check for proper alignment and clearance of the air springs. Improper alignment or inadequate clearance can cause the air springs to rub against other components, leading to premature wear and potential failure. Ensure that the air springs are installed in the correct position and that there is sufficient clearance in all directions. This will help to prevent any unnecessary stress on the air springs and prolong their lifespan.
By following these tips and best practices for proper installation, you can extend the lifespan of your air springs and maximize their durability. Remember to always consult the manufacturer’s guidelines and instructions for specific installation requirements. Proper installation is an investment in the longevity and performance of your air springs, ultimately saving you time and money in the long run.
Choosing the Right Air Springs for Heavy Truck Applications
The choice of air springs for heavy truck applications is crucial to ensure optimal performance and durability. With the ever-increasing demands and challenges faced by heavy trucks, selecting the right air springs becomes even more important. Various factors must be considered, such as load capacity, operating conditions, and compatibility with the truck’s suspension system. Making an informed decision will not only enhance the overall performance of the truck but also contribute to extending the lifespan of the air springs.
When choosing air springs for heavy truck applications, one of the key factors to consider is the load capacity. Heavy trucks are designed to carry significant loads, and the air springs must be able to support these weights effectively. It is essential to check the load capacity rating of the air springs and ensure that it matches the requirements of the specific truck. Overloading the air springs can lead to premature wear and potential failure, compromising both safety and performance.
Operating conditions also play a vital role in selecting the right air springs for heavy truck applications. Trucks operate in various environments and encounter different road conditions. Some trucks may primarily operate on highways, while others may frequently navigate rough terrain or off-road paths. It is important to consider factors such as vibration, shock absorption, and temperature variations when choosing air springs. The air springs should be designed to withstand these conditions and offer optimal performance and durability in the intended operating environment.
In addition to load capacity and operating conditions, compatibility with the truck’s suspension system is another crucial aspect to consider when selecting air springs. Each truck has a unique suspension system, and the air springs must be compatible with it to ensure proper installation and functioning. It is recommended to refer to the truck manufacturer’s guidelines or consult with experts to determine the compatibility of different air spring options with the specific truck’s suspension system.
To summarize, choosing the right air springs for heavy truck applications requires careful consideration of factors such as load capacity, operating conditions, and compatibility with the truck’s suspension system. By making an informed decision, truck owners and operators can enhance the overall performance, durability, and lifespan of the air springs, ultimately contributing to a safer and more efficient heavy trucking industry.
Case Studies: Successful Strategies for Enhancing Air Spring Durability
When it comes to enhancing the durability of air springs, there are various strategies that can be employed. One effective approach is to analyze case studies of successful applications, where air spring durability has been maximized. By examining real-world examples, valuable insights can be gained, enabling manufacturers and users to optimize the lifespan and performance of air springs.
One important factor to consider in enhancing air spring durability is material selection. The choice of materials can significantly impact the longevity and reliability of air springs. Factors such as abrasion resistance, flexibility, and chemical compatibility should be carefully evaluated. Case studies have demonstrated that selecting materials with superior durability characteristics, such as high-quality elastomers and reinforced fabrics, can greatly enhance the lifespan of air springs.
Air spring durability is also affected by the specific application and the loads it encounters. Heavy truck loads, for instance, can exert significant stress on air springs, leading to wear and potential failure. In successful case studies, it has been observed that employing air springs specifically designed for heavy truck applications can greatly enhance durability. These specialized air springs are engineered to withstand higher loads and provide optimal performance under demanding conditions.
Factors Affecting Air Spring Durability | Strategies for Enhancing Durability |
---|---|
Material Selection | Selecting high-quality elastomers and reinforced fabrics |
Application-specific Design | Choosing air springs specifically designed for heavy truck loads |
Maintenance Practices | Implementing regular inspections and maintenance routines |
In addition to material selection and application-specific design, maintenance practices play a crucial role in enhancing air spring durability. Case studies have consistently shown that implementing regular inspections and maintenance routines can significantly extend the lifespan of air springs. Simple practices such as checking for leaks, monitoring air pressure, and lubricating moving parts can prevent premature wear and potential failures.
By analyzing case studies and implementing successful strategies, it is possible to enhance the durability of air springs. Material selection, application-specific design, and proper maintenance practices all contribute to maximizing the lifespan and performance of air springs. Manufacturers and users alike should strive to incorporate these strategies to ensure the longevity and reliability of their air springs.