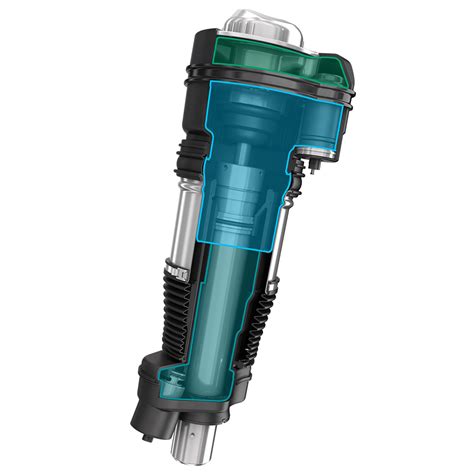
Introduction to Air Spring Systems
Air spring systems have become increasingly popular in various industries due to their unique advantages and versatile applications. These systems utilize compressed air as the primary medium to provide support, cushioning, and isolation in a wide range of mechanical and suspension applications. From automotive and heavy machinery industries to aerospace and even healthcare, air spring systems offer numerous benefits over traditional spring and shock absorber systems. In this blog post, we will explore the different types of air spring systems, their advantages, components, working principles, and maintenance tips. We will also discuss common issues that may arise with these systems and explore future innovations in this exciting technology.
Introduction to Air Spring Systems
An air spring system is a type of suspension system used in vehicles to provide support and cushioning. Unlike traditional coil or leaf spring systems, air spring systems use air-filled chambers to absorb shocks and vibrations. These systems are commonly used in heavy-duty vehicles such as trucks, buses, and trailers, as well as in certain types of passenger cars.
There are several types of air spring systems available in the market, each designed for specific applications. The most common type is the convoluted air spring, which features a bellows-like structure made of flexible rubber or elastomer material. Another type is the rolling lobe air spring, which consists of a cylindrical air chamber and a piston that rolls along the inner surface of the chamber. Additionally, there are also air bag systems, which are used in air suspension kits for aftermarket customization of vehicles.
One of the main advantages of air spring systems is their ability to provide a smooth and comfortable ride. The adjustable nature of these systems allows for varying load capacities and ride heights, making them ideal for vehicles that frequently carry heavy loads. Moreover, air springs are known for their superior vibration isolation properties, making them suitable for applications where ride comfort is a priority.
- Superior ride comfort
- Adjustable load capacity and ride height
- Improved vibration isolation
Component | Description |
---|---|
Air spring | The main component that holds pressurized air and provides support and cushioning. |
Air compressor | Responsible for pressurizing the air inside the air spring. |
Control valves | Regulate the flow of air between the air springs and the compressor. |
Air reservoir | Stores compressed air for future use. |
Maintaining an air spring system is relatively easy. Regular inspection of the components and checking for any signs of wear and tear is important. It is also crucial to keep the air springs properly inflated to ensure optimal performance and prevent any potential issues. Additionally, following the manufacturer’s recommended maintenance schedule and guidelines is essential for prolonging the lifespan of the system.
While air spring systems offer many advantages, they are not without their common issues. Over time, air springs may develop leaks or become damaged, resulting in air leakage and loss of suspension performance. The air compressor and control valves can also experience failures, leading to improper pressurization or unresponsiveness of the system. Timely repairs and replacements are necessary to address these issues and maintain the functionality of the system.
Air spring systems find applications in a wide range of industries and vehicles. They are commonly used in heavy-duty trucks and buses, where the ability to carry heavy loads and provide a comfortable ride is crucial. In addition, air springs are also used in luxury cars and recreational vehicles to enhance ride quality. Furthermore, these systems are employed in specialized vehicles such as fire trucks, ambulances, and military vehicles, where stability and load-carrying capabilities are essential.
The future of air spring systems looks promising, with continuous innovations in materials and technology. Manufacturers are exploring advanced materials that offer improved durability and performance. Additionally, the integration of electronic control systems and adaptive suspension technologies is expected to further enhance the capabilities and versatility of air spring systems, providing even greater ride comfort and stability in various applications.
Types of Air Spring Systems
There are several types of air spring systems that are widely used in various applications. These systems provide a reliable and efficient way to handle suspension and vibration control in different industries. In this blog post, we will discuss some of the most common types of air spring systems and their characteristics.
1. Rolling Lobe Air Springs: This type of air spring consists of a flexible member called a rolling lobe, which is usually made of rubber. It is designed to accommodate both vertical and longitudinal forces and provides a high level of isolation. Rolling lobe air springs are commonly used in the transportation industry, particularly in trucks, buses, and trailers, for smooth and comfortable rides.
2. Sleeve Air Springs: Sleeve air springs, also known as bellows air springs, are designed with a cylindrical-shaped elastomeric tube, which expands and contracts to provide the necessary suspension support. These air springs are known for their high load capacity and are commonly used in heavy-duty applications such as railway carriages, mining equipment, and industrial machinery.
3. Convolute Air Springs: Convolute air springs have a convoluted shape, resembling an accordion. These air springs are built to withstand heavy loads and provide excellent vibration isolation. They are commonly used in the automotive industry for passenger cars, light trucks, and SUVs, providing enhanced comfort and stability.
4. Rolling Sleeve Air Springs: Rolling sleeve air springs combine the advantages of rolling lobe and sleeve air springs. They feature a rolling sleeve design with an added internal piston, allowing for a greater range of motion and improved load-carrying capacity. Rolling sleeve air springs find applications in various industries, including agriculture, construction, and off-road vehicles.
Comparison of Different Types of Air Spring Systems:Type | Characteristics | Applications |
---|---|---|
Rolling Lobe | Vertical and longitudinal forces, high isolation | Trucks, buses, trailers |
Sleeve | High load capacity | Railway carriages, mining equipment, industrial machinery |
Convolute | Heavy loads, excellent vibration isolation | Passenger cars, light trucks, SUVs |
Rolling Sleeve | Greater range of motion, improved load-carrying capacity | Agriculture, construction, off-road vehicles |
Each type of air spring system has its own unique advantages and applications. The choice of the appropriate air spring system depends on the specific requirements of the vehicle or equipment it will be used in. By understanding the different types of air spring systems available, you can make informed decisions and ensure optimal performance in your suspension and vibration control needs.
Advantages of Air Spring Systems
Air spring systems have gained popularity as a reliable and efficient solution for various applications. They are widely used in industries such as automotive, transportation, and heavy machinery. In this blog post, we will explore the numerous advantages of air spring systems and why they are being preferred over traditional spring systems.
1. Enhanced Comfort: One of the significant advantages of air spring systems is their ability to provide a smoother and more comfortable ride. The air springs can absorb shocks and vibrations, resulting in reduced body roll and improved stability. This feature is especially beneficial for vehicles used in long-distance transportation.
2. Adjustable Suspension: Air spring systems offer the advantage of adjustable suspension. By varying the air pressure in the springs, the height and firmness of the suspension can be easily altered. This allows the driver to customize the ride quality according to their preference, making it suitable for different road conditions and loads.
3. Increased Load Capacity: Another significant advantage of air spring systems is their ability to handle heavy loads. The air springs can support more weight compared to traditional springs, making them ideal for commercial vehicles, heavy-duty machinery, and cargo transportation. The increased load capacity enhances safety and prevents excessive wear and tear on the vehicle.
4. Improved Fuel Efficiency: Air spring systems can contribute to improved fuel efficiency. The use of air springs reduces friction and eliminates the need for additional components such as shock absorbers. This reduction in weight and drag leads to better fuel economy, making air spring systems a cost-effective choice for vehicle owners.
5. Noise and Vibration Damping: Air spring systems excel in minimizing noise and vibration. They are designed to dampen vibrations and isolate the vehicle’s chassis from bumps and road irregularities, resulting in a quieter and more comfortable ride. This advantage is particularly crucial for luxury vehicles and high-end transportation services.
6. Longer Service Life: Air spring systems are known for their durability and extended service life. The use of high-quality materials and advanced manufacturing techniques ensures that they can withstand harsh operating conditions and resist corrosion. This longevity reduces maintenance and replacement costs, making air spring systems a cost-effective investment.
In conclusion, air spring systems offer numerous advantages that make them a preferred choice for various applications. From enhanced comfort and adjustable suspension to increased load capacity and improved fuel efficiency, these systems provide a range of benefits. Moreover, their ability to dampen noise and vibrations and their longer service life add to their appeal. As technology continues to evolve, we can expect further innovations and enhancements in air spring systems, making them even more reliable and efficient in the future.
Components of an Air Spring System
An air spring system is a type of suspension system that uses compressed air to provide cushioning and support to a vehicle. It is commonly used in heavy-duty vehicles such as trucks, buses, and trailers. A typical air spring system consists of several components that work together to provide a comfortable and stable ride. In this article, we will discuss the key components of an air spring system and their functions.
1. Air Spring: The air spring is the main component of the system and is responsible for supporting the weight of the vehicle. It is made of a flexible and airtight rubber or synthetic material. The air spring is designed to inflate or deflate according to the load on the vehicle, providing a smooth and controlled ride.
2. Air Compressor: The air compressor is responsible for supplying compressed air to the air spring. It pressurizes the air and sends it to the air spring through a series of pipes or hoses. The compressor is usually driven by the vehicle’s engine or an electric motor.
3. Control Valve: The control valve is used to regulate the flow of air into and out of the air spring. It is typically controlled by the vehicle’s suspension management system, which adjusts the air pressure in the air spring according to the driving conditions and load on the vehicle. The control valve ensures that the air spring maintains the correct level of stiffness and provides proper suspension performance.
4. Air Reservoir: The air reservoir is a storage tank for compressed air. It is connected to the air compressor and provides a reserve of air for the system. The air reservoir helps to maintain a steady supply of air to the air spring, especially during sudden changes in load or when the compressor is not actively pumping air.
5. Air Lines and Fittings: The air lines and fittings connect the various components of the air spring system, allowing the flow of compressed air. They are usually made of durable materials such as rubber or metal and are designed to withstand high pressure and vibrations.
In conclusion, an air spring system consists of several important components that work together to provide a reliable and efficient suspension system. The air spring, air compressor, control valve, air reservoir, and air lines play crucial roles in maintaining the stability, comfort, and performance of the vehicle. Understanding the components of an air spring system can help vehicle owners and mechanics diagnose and address any issues that may arise, ensuring a smooth and safe ride.
Working Principle of Air Spring Systems
An air spring system is a type of suspension system that uses compressed air to support and cushion the weight of a vehicle or machinery. It is commonly used in heavy-duty vehicles, such as trucks and buses, as well as industrial equipment. The working principle of air spring systems involves the release and compression of air within the spring to provide a smooth and comfortable ride. Let’s take a closer look at how these systems work and what makes them unique.
Release and Compression of Air
One of the key components of an air spring system is the air spring itself, which consists of a flexible and airtight bag made of synthetic rubber or polyurethane. When the vehicle or machinery is in motion, the weight is transferred onto the air spring, causing it to compress. This compression results in the release of air from the spring, which helps absorb vibrations, shocks, and bumps on the road. The air spring adjusts the amount of air released according to the weight and condition of the vehicle, ensuring a comfortable and stable ride.
Adjustable and Adaptive
An important feature of air spring systems is their ability to be adjustable and adaptive. By varying the amount of air in the spring, the system can be customized to meet different load requirements. This allows the suspension to maintain optimal performance regardless of the payload or road conditions. The adaptability of air spring systems ensures better control, stability, and overall safety, especially in heavy-duty applications where the load can vary significantly.
Advantages of Air Spring Systems
- Improved ride comfort: Air spring systems provide a smoother and more comfortable ride compared to traditional suspension systems. The ability to absorb shocks and bumps reduces the impact felt by the passengers or operators.
- Enhanced load-carrying capability: The adjustable nature of air spring systems allows for better load distribution and increased carrying capacity. This is particularly beneficial in commercial vehicles and heavy machinery.
- Reduced wear and tear: The cushioning effect of air springs helps minimize the wear and tear on the vehicle’s components and suspension system. This leads to longer service life and reduced maintenance costs.
In conclusion, air spring systems offer a unique working principle that provides superior ride comfort, adaptability, and numerous advantages over traditional suspension systems. Their ability to adjust according to the load requirements ensures optimal performance and safety. With ongoing advancements and future innovations, air spring systems are expected to play a significant role in the automotive and industrial sectors.
Maintenance Tips for Air Spring Systems
When it comes to maintaining air spring systems, there are a few key tips to keep in mind to ensure their longevity and optimal performance. Air spring systems are commonly used in various industries, including automotive, railway, and aerospace, due to their ability to provide a smooth and comfortable ride. By following these maintenance tips, you can keep your air spring systems in top shape, saving time and money in the long run.
First and foremost, it is essential to regularly inspect your air spring systems for any signs of wear or damage. This includes checking for cracks, leaks, or any visible deterioration in the materials. By identifying and addressing these issues early on, you can prevent further damage and potential system failure.
Another crucial maintenance tip is to ensure proper air pressure levels in the system. Adequate air pressure is essential for the functionality and performance of air spring systems. It is recommended to monitor the air pressure regularly and adjust it as needed to maintain the desired level of support and load-bearing capacity. Refer to the manufacturer’s guidelines or recommendations for the specific air spring system you are using.
- Regular cleaning and lubrication: Keeping the air spring components clean and well-lubricated is key to their longevity and smooth operation. Remove any dirt or debris that may accumulate and hinder the functionality of the system. Additionally, apply suitable lubricants to the moving parts and joints to minimize friction and ensure proper movement.
- Protect from extreme temperatures: Air spring systems can be sensitive to extreme temperatures, both hot and cold. It is crucial to store and operate the systems within the recommended temperature range to prevent damage. Extreme temperatures can affect the performance and efficiency of the system, so it is essential to consider the environmental conditions in which the air spring systems are used.
- Regular inspection of mounting components: The mounting components, such as brackets and bolts, play a vital role in the stability and effectiveness of air spring systems. Regularly inspect these components for any signs of wear, corrosion, or looseness. Address any issues promptly by replacing or tightening the affected parts to maintain the integrity of the system.
Benefits of Maintenance Tips for Air Spring Systems |
---|
1. Prolongs the lifespan of the air spring system. |
2. Avoids costly repairs or replacements. |
3. Ensures optimal performance and functionality. |
4. Reduces the risk of system failure and related accidents. |
5. Improves safety and comfort for users. |
By following these maintenance tips for air spring systems, you can ensure their reliable performance, extend their lifespan, and avoid unnecessary repairs or replacements. Regular inspection, proper air pressure management, cleaning, lubrication, and protection from extreme temperatures are essential aspects of maintaining air spring systems. Taking the time to care for your air spring systems will not only save you time and money but also contribute to a safer and more comfortable experience for users.
Common Issues with Air Spring Systems
When it comes to air spring systems, there are a few common issues that can arise. These systems are designed to provide a cushion of air between the vehicle’s suspension and the road surface, helping to improve ride comfort and stability. However, like any mechanical system, air springs can experience problems over time. It’s important to be aware of these common issues, so you can address them promptly and ensure the longevity and performance of your air spring system.
One common issue with air spring systems is air leakage. Over time, the air springs can develop small leaks, leading to a gradual loss of air pressure. This can result in a decrease in ride comfort and suspension performance. To identify any air leaks, you can visually inspect the air springs for any signs of damage or wear. Additionally, you can spray a soapy water solution onto the air springs and look for any bubbles, which would indicate a leak. If a leak is detected, it’s important to have it repaired or replaced to maintain the optimal functioning of the air spring system.
Another common issue is uneven air distribution among the air springs. In some cases, one or more air springs may not be receiving the same amount of air pressure as the others. This can lead to an imbalance in the suspension system, resulting in uneven ride height and handling characteristics. To address this issue, it’s important to ensure that the air distribution valves are functioning properly and properly regulating the air pressure to each air spring. Regular inspection and maintenance of these valves can help prevent this issue from occurring.
- Air leakage: Over time, air springs can develop small leaks, causing a gradual loss of air pressure. Inspect the air springs for any signs of damage or wear, and use a soapy water solution to identify any leaks.
- Uneven air distribution: In some cases, one or more air springs may not receive the same amount of air pressure as the others, leading to an imbalance in the suspension system. Regularly inspect and maintain the air distribution valves to prevent this issue.
Common Issues | Possible Causes | Solutions |
---|---|---|
Air leakage | Damage or wear in the air springs | Repair or replace the air springs |
Uneven air distribution | Malfunctioning air distribution valves | Inspect and maintain the valves regularly |
Applications of Air Spring Systems
Air spring systems are becoming increasingly popular in various industries due to their numerous benefits. These systems find their applications in a wide range of sectors, ranging from automotive and transportation to industrial and construction. In this blog post, we will explore the different applications of air spring systems and how they enhance performance and efficiency in various industries.
1. Automotive Industry: One of the primary applications of air spring systems is in the automotive industry. These systems are commonly used in commercial vehicles, such as buses and trucks, to improve ride comfort and stability. Air springs help absorb shocks and vibrations, providing a smoother ride for the passengers and reducing fatigue for the driver. Additionally, air springs can adjust the vehicle’s height, allowing for better load distribution and improved handling.
2. Railways and Transportation: Air spring systems also play a significant role in the railway and transportation sector. They are used in rail vehicles, such as passenger trains and metro cars, to provide a comfortable and safe ride. Air springs help to dampen vibrations and reduce noise, enhancing the overall passenger experience. Moreover, these systems contribute to the stability and suspension of the train, ensuring a smoother and more controlled journey.
3. Industrial and Construction: Another vital application of air spring systems is in industrial and construction equipment. These systems are commonly found in heavy-duty machinery, such as cranes, loaders, and excavators. Air springs help to support and isolate the equipment from external shocks and vibrations, ensuring smoother operation and reducing wear and tear. They also improve stability and safety during lifting and carrying heavy loads.
4. Marine and Offshore: Air spring systems are even utilized in marine and offshore applications. They are used in ships and offshore platforms to provide stability and reduce the impact of waves and movements. Air springs help to minimize motion sickness, improve passenger comfort, and facilitate safe operations in harsh sea conditions. These systems also contribute to the effective isolation of onboard equipment, reducing the risk of damage.
Overall, the applications of air spring systems are diverse and widespread. From vehicles and transportation to industrial machinery and marine applications, these systems offer numerous advantages, including enhanced comfort, improved stability, reduced vibrations, and increased safety. With the continuous advancements in technology, we can expect air spring systems to find even more innovative applications in the future.
Future Innovations in Air Spring Systems
As technology continues to advance, so does the development of air spring systems. These innovative systems are constantly being improved upon to provide better performance, increased efficiency, and enhanced durability. The future holds exciting possibilities for the further advancement of air spring systems, with several key areas of innovation on the horizon.
1. Smart Air Spring Systems
One of the future innovations in air spring systems is the integration of smart technology. These smart air spring systems would be equipped with sensors and actuators, allowing for real-time monitoring and adjustment of the suspension performance. The sensors would measure various parameters such as load, height, and pressure, while the actuators would control the air pressure and stiffness of the system. This level of intelligence would enable the air spring systems to adapt to different road conditions and driving styles, providing an optimal balance between comfort and handling.
2. Energy Recovery Systems
Another exciting innovation in air spring systems is the potential utilization of energy recovery systems. These systems would incorporate mechanisms to capture and store energy that is typically dissipated as heat during suspension movements. By harnessing this energy, air spring systems could potentially power additional vehicle components or even recharge the vehicle’s battery. This would not only improve the overall efficiency of the system but also contribute to reducing the vehicle’s environmental impact.
3. Adaptive Materials
The development of adaptive materials is yet another area of future innovation in air spring systems. These materials would possess the ability to change their physical properties in response to external stimuli such as temperature, pressure, or electric fields. By incorporating adaptive materials into the construction of air springs, the system’s performance could be further optimized. For example, the stiffness of the springs could be automatically adjusted based on the road conditions or driver’s preferences, resulting in a more comfortable and dynamic ride.
Conclusion
The future of air spring systems looks promising, with several exciting innovations on the horizon. Smart air spring systems, energy recovery systems, and adaptive materials are just a few areas where advancements are expected. These innovative technologies have the potential to greatly enhance the performance, efficiency, and sustainability of air spring systems, ultimately leading to a better driving experience for vehicle owners.